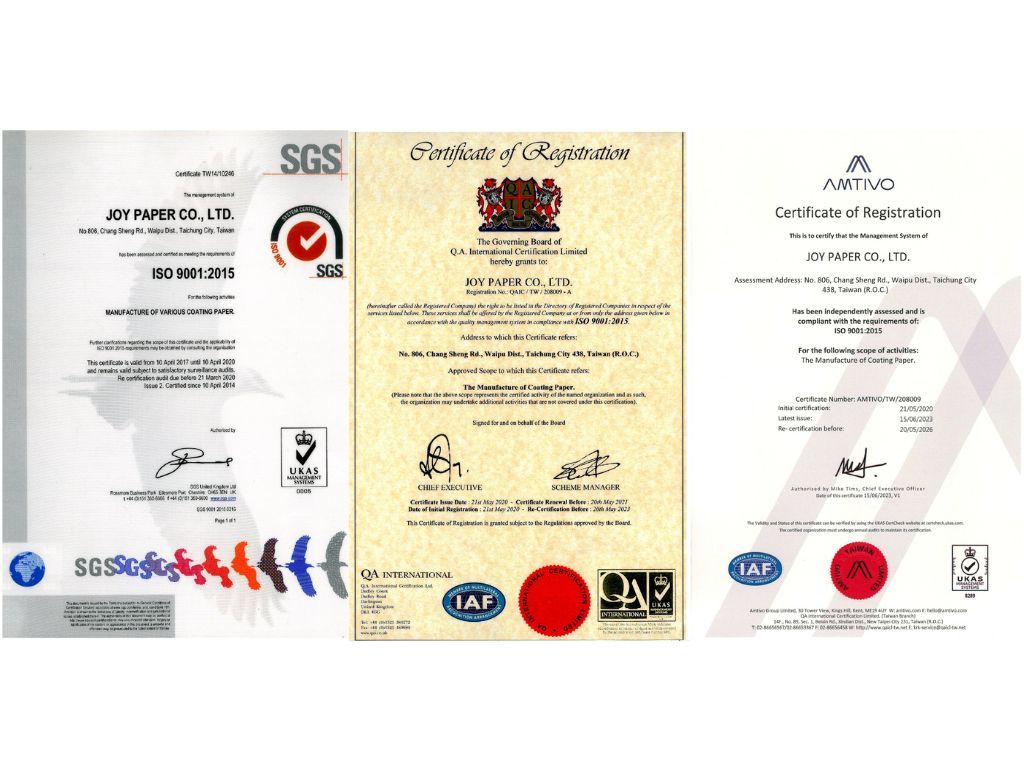
Quality Management
ISO 9001 certified
As a professional coating manufacturer, we are dedicated to producing high-quality products while continuously strengthening our process management and quality control systems. Utilizing a variety of coating technologies, we manufacture a wide range of products, including food packaging materials (such as paper cups, food containers, burger wrappers, and steamer paper), as well as release liners for labels and adhesive tapes. All of our coated papers are developed through a high-precision coating platform, supported by a rigorous quality management system, standardized SOP workflows, and comprehensive staff training. With an average monthly yield rate of 96.2%, we effectively reduce waste and enhance overall production efficiency.
To ensure product consistency and stability, we have introduced advanced testing equipment and strict quality verification procedures. We firmly believe that quality is the cornerstone of sustainable business, and we continuously optimize our processes and refine our technologies to provide the most reliable solutions for our customers. Customer satisfaction and trust are the driving forces behind our ongoing progress.
On the production floor, we conduct strict quality control over all incoming raw materials, which are widely used in products such as PE-coated packaging paper, glassine release liners, and kaolin-coated paper. According to standardized inspection procedures and specifications, we use electronic scales to measure basis weight and thickness gauges to verify caliper, ensuring all materials meet production standards. As the first step in quality management, incoming material inspection plays a crucial role in improving product yield and maintaining stable production processes.
After the coating process is completed, each batch of paper undergoes a series of precise quality inspections. First, we use X-ray equipment to measure the coating weight on the paper surface, ensuring the release agent is applied within standard levels and that release performance remains stable. Second, we perform aging peel tests using FINAT 10 international standards in combination with an oven, converting release force into data to evaluate whether the product meets customer specifications. Finally, we conduct a dye-test using red ink to assess the coverage of the release agent. This step helps us detect any uneven application that could result in adhesion issues.
In the final packaging stage, we also inspect the product’s appearance, labeling, marking, and quantity to ensure every batch meets shipping standards—delivering consistent and reliable quality to our customers.
Below is the introduction of the instruments:
- Electronic Balance: used to measure the basis weight of the paper.
- Thickness Tester: utilized to measure the thickness of the paper.
- Tensile Testing Machine: employed according to international standard FINAT10 to measure release force.
- XRF Analyzer: utilized for X-ray detection of coating weight on the paper surface.
- Dye-test: use red ink to check the uniformity of release agent on the paper surface.
- Oven: Using fixed-time heating to simulate aging conditions to observe changes in release force over time.